Расскажем из чего делают кузова автомобилей и какие технологии появились? Рассмотрим недостатки и преимущества основных материалов, используемых при изготовлении машины.
Для изготовления кузова необходимо сотни отдельных частей, которые затем нужно соединить в одну конструкцию, соединяющую все части современного автомобиля. Для легкости, прочности, безопасности и минимальной стоимости кузова конструкторам необходимо идти на компромиссы, искать новые технологии, новые материалы.
Сталь
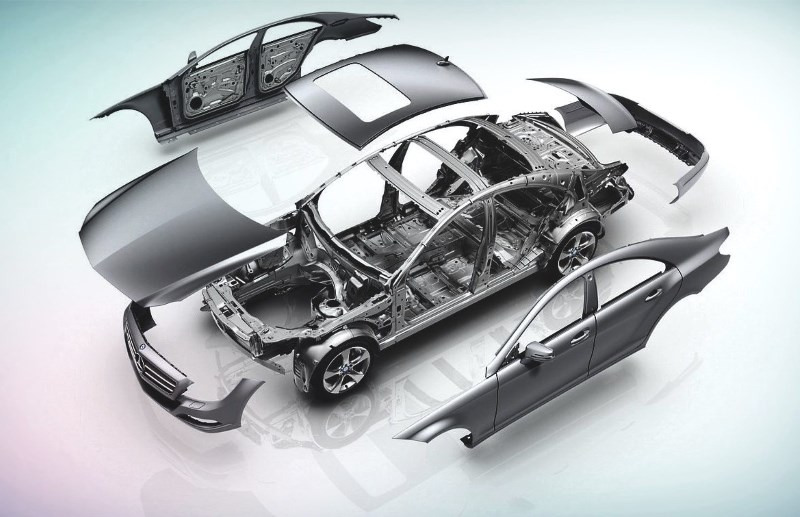
Основные детали кузова изготовляют из стали, алюминиевых сплавов, пластмасс и стекла. Причем предпочтение отдается низкоуглеродистой листовой стали толщиной 0,65...2 мм. Благодаря применению последней удалось снизить общую массу машины и повысить жесткость кузова. Это вызвано ее высокой механической прочностью, недефицитностью, способностью к глубокой вытяжке (можно получать детали сложной формы), технологичностью соединения деталей сваркой. Недостатками этого материала являются высокая плотность и низкая коррозионная стойкость, требующая сложных мероприятий по защите от коррозии.
Конструкторам нужно, чтобы сталь была прочной и обеспечивала высокий уровень пассивной безопасности, а технологам нужна хорошая штампуемость. И главная задача металлургов - угодить и тем и другим. Поэтому разработан новый сорт стали, позволяющий упростить производство и в дальнейшем получить заданные свойства кузова.
Изготавливается кузов в несколько этапов. С самого начала изготовления из стальных листов, имеющих разную толщину, штампуются отдельные детали. После эти детали свариваются в крупные узлы и с помощью сварки собираются в одно целое. Сварку на современных заводах ведут роботы.
Преимущества:
- низкая стоимость;
- высокая ремонтопригодность кузова;
- отработанная технология производства и утилизации.
Недостатки:
- самая большая масса;
- требуется антикоррозийная защита от коррозии;
- потребность в большом количестве штампов;
- ограниченный срок службы.
Что в будущем? Совершенствование технологий производства и штамповки, увеличение в структуре кузова доли высокопрочных сталей. И применение сверхвысокопрочных сплавов нового поколения. К ним уже можно отнести TWIP-сталь с высоким содержанием марганца (до 20%). Данная сталь обладает особым механизмом пластической деформации, благодаря которому относительное удлинение может достигать 70%, а предел прочности - 1300 МПа. Для примера: прочность обычных сталей составляет до 210 МПа, а высокопрочных - от 210 до 550 МПа.
Алюминий
Алюминиевые сплавы для изготовления автомобильных кузовов начали использовать относительно недавно. Используют алюминий при изготовлении всего кузова или его отдельных деталей – капот, двери, крышка багажника.
Алюминиевые сплавы применяются в ограниченном количестве. Поскольку прочность и жесткость этих сплавов ниже, чем у стали, поэтому толщину деталей приходится увеличивать и существенного снижения массы кузова получить не удается. Кроме того, шумоизолирующая способность алюминиевых деталей ниже, чем стальных, и требуются более сложные мероприятия для достижения акустической характеристики кузова.
Начальный этап изготовления алюминиевого кузова схожий с изготовлением стального. Детали вначале штампуются из листа алюминия, потом собираются в целую конструкцию. Сварка используется в среде аргона, соединения на заклепках и/или с использованием специального клея, лазерная сварка. Также к стальному каркасу, который изготовлен из труб разного сечения, крепятся кузовные панели.
Достоинства:
- возможность изготовить детали любой формы;
- кузов легче стального, при этом прочность равная;
- легкость в обработке, вторичная переработка не составляет труда;
- устойчивость к коррозии, а также низкая цена технологических процессов.
Недостатки:
- низкая ремонтопригодность;
- необходимость в дорогостоящих способах соединения деталей;
- необходимость специального оборудования;
- значительно дороже стали, так как энергозатраты намного выше.
Стеклопластик и пластмассы
Под названием стеклопластик имеется в виду любой волокнистый наполнитель, который пропитан полимерными смолами. Наиболее известными наполнителями считаются – карбон, стеклоткань и кевлар.
Около 80% пластмасс, применяемых в автомобилях, приходится на пять типов материалов: полиуретаны, поливинилхлориды, полипропилены, АБС-пластики, стеклопластики. Остальные 20% составляют полиэтилены, полиамиды, полиакрилаты, поликарбонаты.
Из стеклопластиков изготовляют наружные панели кузовов, что обеспечивает существенное уменьшение массы автомобиля. Из полиуретана делают подушки и спинки сидений, противоударные накладки. Сравнительно новым направлением является применение этого материала для изготовления крыльев, капотов, крышек багажника.
Поливинилхлориды применяют для изготовления многих фасонных деталей (щиты приборов, рукоятки) и обивочных материалов (ткани, маты). Из полипропилена делают корпуса фар, рулевые колеса, перегородки и многое другое. АБС-пластики используют для различных облицовочных деталей.
Достоинства стеклопластика:
- при высокой прочности маленький вес;
- поверхность деталей обладает хорошими декоративными качествами;
- простота в изготовлении деталей, имеющих сложную форму;
- большие размеры кузовных деталей.
Недостатки стеклопластика:
- высокая стоимость наполнителей;
- высокое требование к точности форм и к чистоте;
- время изготовления деталей достаточно продолжительное;
- при повреждениях сложность в ремонте.
Автомобильная промышленность не стоит на месте и развивается в угоду потребителю, который хочет быстрый и безопасный автомобиль. Это приведет к тому, что в производстве авто используются новые, отвечающие современным требованиям материалы.
|